За способом одержання числового значеннявимірюваної величини вимірювання поділяються на прямі, посередні, сукупніта сумісні.
Класифікація вимірювань
На результати вимірювань впливає досить багато чинників: зовнішні умови, методи, технічні засоби вимірювання, стан експериментатора та ін. Зважаючи на численність різних чинників та умов проведення експерименту, вимірювання можна класифікувати за характером зміни вимірюваної величини в часі, за способом одержання числового значення, точністю та ін.
За характером зміни вимірюваної величини в часі вимірювання можна розділити на статичні та динамічні.
Статичні вимірювання — це вимірювання, при яких протягом певного проміжку часу вимірювана величина майже не змінюється або ж її значення змінюється поступово відповідно до процесу виробництва. Статичні вимірювання (рис. 1) використовуються, як правило, для встановлення взаємозв'язку між фізичними величинами одного і того самого об'єкта дослідження. Вони застосовуються у пасивних експериментах і забезпечують задовільний рівень наочності при зміні вимірюваних величин за певний проміжок часу (годину, зміну, добу). Таким, наприклад, є проведення пасивного експерименту на випарній установці для вимірювання основних її параметрів: температури, рівня, тиску, витрати пари тощо.
Рис. 1. Статичні характеристики вимірюваних величин — тиску, температури та рівня за проміжок часу т
Динамічні вимірювання — вимірювання, які показують зміну вимірюваної величини в часі при різних збуреннях, що впливають на об'єкт дослідження або ж на засіб вимірювання. Динамічні вимірювання дають можливість вивчати
Змін. |
Арк. |
№ докум. |
Підпис |
Дата |
Арк. |
На рис. 2 показано перехідний процес вимірюваної величини Хд у часі т при різкій зміні вимірюваної величини на вході приладу. Як видно з графіка, показання приладу Уд досягають сталого значення У лише через певний час і наближаються до нього поступово відповідно до експоненціального закону. Різниця між показаннями приладу Уд і дійсним значенням вимірюваної величини У називається динамічною похибкою:д = У-Уд. На графіку (рис. 2) показані параметри, які характеризують динаміку процесу вимірювання.
Рис. 2. Динамічна характеристика вимірюваної величини
Час початку реагування п— час від початку зміни вимірюваної величини на вході приладу до початку зміни показів приладу (значення вихідного сигналу).
Час перехідного процесу Tпп — час, протягом якого показання приладу після початку зміни вхідної вимірюваної величини досягнуть значення з 5-процентним відхиленням (Хд=0,95).
Повний час встановлення значення вимірюваної величини Тпп — час, протягом якого значення вимірюваної величини досягає свого сталого значення від початку зміни вхідної величини на вході приладу.
Постійна часу Т— час, протягом якого вихідна вимірювана величина досягає 0,632 свого сталого значення на виході приладу, тобто це час перехідного процесу, який описується рівнянням експоненти.
У загальному випадку для опису лінійних вимірювальних засобів використовуються лінійні диференціальні рівняння. Якщо ж вимірювальний засіб має нелінійні елементи, то їх характеристики можна лінеаризувати, тобто
Змін. |
Арк. |
№ докум. |
Підпис |
Дата |
Арк. |
an(dny/dn) + an-1(dn-1y/dn-1) + . . + a1(dy/d) + a0y = bm(dmx/dm) +
+ bm-1(dm-1x/dm-1) + . + b1(dx/d) + b0x. (4)
Поряд з диференціальними рівняннями для опису динаміки перехідних процесів вимірювальних систем доцільно використовувати передаточні функції. Динамічні характеристики засобів вимірювання, які характеризують їх реакцію на гармонійні коливання у широкому діапазоні частот, називають частотними характеристиками, які містять в собі амплітудно-частотні та фазочастотні характеристики. Частотні характеристики можна одержати як експериментально, так і розрахунковим шляхом.
За способом одержання числового значеннявимірюваної величини вимірювання поділяються на прямі, посередні, сукупніта сумісні.
Прямиминазиваються такі вимірювання, за яких значення вимірюваної величини визначається безпосередньо за експериментальними даними (вимірювання довжини метром, вимірювання температури термометром, тиску манометром та ін.). Прямі вимірювання найпростіші і найпоширеніші у промисловості.
Посередніминазиваються такі вимірювання, за яких значення вимірюваної величини визначається за допомогою відомих математичних залежностей між цією величиною і величиною, яка визначається прямими вимірюваннями. Наприклад: визначення об'єму рідини у циліндричній посудині за висотою рідини в ній та площею дна S - V = Sh; густини рідини за масою і її об'ємом — р = m/V та ін.
У загальному вигляді вимірювана величина визначається за формулою
X=f(y1,y2,y3 .), (5)
Змін |
Арк. |
№ документа |
Підпис |
Дата |
Аркуш |
Розробив |
Перевірив |
Н. Контр. |
Затвердив |
Літера |
Аркушів |
Розмітка і рубання металу
Рубкою називається слюсарна операція, при якій з допомогою ріжучого інструменту (зубила) з заготовки або деталі видаляють зайві шари металу або заготовку розрубують на частини.
При сучасних способах обробки матеріалу або заготовок рубка металу є підсобної операцією.
Рубання металу виробляють в лещатах, на плиті і на ковадлі з допомогою слюсарного молотка, слюсарного зубила, крейцмейселя, ковальського зубила і кувалди.
Рубка металу буває горизонтальна і вертикальна в залежно від розташування зубила під час операції. Горизонтальну рубку виробляють в лещатах. При цьому задню грань зубила встановлюють до площини губок лещат майже горизонтально, під кутом не більше 5°. Вертикальну рубку виконують на плиті або ковадлі. Зубило встановлюють вертикально, а перерубаемый матеріал укладають на плиті горизонтально.
Для слюсарної рубання застосовують молотки масою 400, 500, 600 і 800 р. Молотки насаджують на ручки з дерева твердих і в'язких порід (береза, клен, дуб, горобина). Ручки повинні бути овальної форми, з гладкою і чистою поверхнею, без сучків і тріщин. Довжина ручки молотка масою 400-600 м дорівнює 350 мм, масою 800 г - 380-450 мм. Щоб молоток під час роботи не зіскакував, кінець ручки, на який насаджений молоток, розклинюють дерев'яними або металевими клинами товщиною 1-3 мм Клини ставлять уздовж великої осі перерізу ручки. Дерев'яні клини ставлять на клею, а металеві заершивают, щоб вони не випадали.
Робочу частину зубила і крейцмейселя- (5, в, г) гартують на довжину не менше 30 мм, а головку гартують слабкіше леза (на довжину близько 15-25 мм), щоб при ударі молотком вона не кришилась і не тріскалася.
Вся інша частина зубила і крейцмейселя повинна залишатися м'якою. Зубила і крейцмейсели не повинні мати тріщин, полон і інших вад.
Найбільш часто використовують зубила довжиною 175 і 200 мм з лезами завширшки 20 і 25 мм. Для прорубання канавок в сталі і чавуні застосовують крейцмейсели довжиною 150-175 мм з лезом шириною 5-10 мм. Головки зубила і крейцмейселя відковують на конус, що забезпечує правильне напрямок удару молотком і зменшує можливість утворення грибоподібної капелюшки на голівці. Кут заточування зубил і крейцмейселей залежить від твердості
Змін. |
Арк. |
№ докум. |
Підпис |
Дата |
Арк. |
Слюсарний інструмент заточують на заточувальних верстатах з абразивними кругами. Під час заточування робоча частина інструмента (лезо) сильно нагрівається і може відбутися її відпустку. При відпуску твердість загартування втрачається і інструмент стає непридатним для подальшої роботи. Щоб уникнути цього робочу частину інструменту під час заточування охолоджують водою. На 6 показано, як треба тримати зубило при заточуванні і як перевіряти правильність заточування кута.
Правила і прийоми рубання металу
Продуктивність і чистота рубки металу залежать від правильних прийомів роботи. При рубці стояти треба стійко і прямо, впівоберта до тискам. Молоток належить тримати за ручку на відстані 15-20 мм від кінця і наносити сильні удари по центру головки зубила. Дивитися слід на лезо зубила, а не на його головку, в іншому випадку лезо зубила піде неправильно. Зубило належить тримати на відстані 20-25 мм від головки.
Заготовки з листової або сортової сталі можна обрубувати в лещатах за рівнем губок або за ризиками понад рівня губок лещат.
При рубанні за рівнем губок лещат (8, а, б) заготовку міцно затискають в лещата так, щоб верхнє ребро виступало понад губок на 3-4 мм і зрубують першу стружку на всю довжину заготовки. Потім заготовку переставляють в лещатах, щоб верхнє ребро виступало на 3-4 мм понад рівень губок лещат, і зрубують другу стружку. Так послідовно обрубують виріб до необхідного розміру.
При рубці понад рівня губок лещат (8, в) за ризиками заготовку затискують у лещата, щоб розмічена ризику була понад рівня губок лещат і паралельна їм. Рубку виробляють по розмічених ризиків послідовно, як і при рубці за рівнем губок лещат. Лезо зубила при рубці повинно бути розташоване під кутом 45° до обрубаемому металу, а головка піднята догори під кутом 25-40°. При такому розташуванні зубила лінія зрубування буде ровцой і рубка буде проводитися швидше.
Великий шар металу на широкій площині заготовки зрубують наступним чином: заготовку затискують у лещата, зубилом обрубують фаску, крейцмейселем прорубують поперечні канавки, а потім зрубують зубилом виступаючі межі. При прорубании канавок крейцмейселем товщина стружки повинна бути не більше 1 мм, а при зрубуванні виступаючих граней зубилом - від 1 до 2 мм.
Смугову сталь перерубують на плиті або наковальня (9). Попередньо на обидві сторони смуги крейдою наносять лінії переруб. Потім, уклавши смугу на ковадло, встановлюють слюсарне зубило вертикально на розміченій ризик і
Змін. |
Арк. |
№ докум. |
Підпис |
Дата |
Арк. |
Круглий метал перерубують таким же чином, з поворотом прутка після кожного удару. Надрубив пруток по всій окружності на достатню глибину, відламують отрубаемую частина.
Вуглецеву і леговану конструкційну сталь товщиною до 20-25 мм можна перерубать в холодному стані на плиті або ковадлі з допомогою ковальських зубил (10, а, б) та кувалд (10, в, г). Для цього на-т*« іпі , Чвтыре сторони заготовки наносять крейдою лінії переруб. Потім укладають метал на ковадлі, встановлюють вертикально ковальське зубило на лінії розмітки і сильними ударами кувалди надрубают метал по всій цій лінії на необхідну глибину, поступово переставляючи зубило. Так само надрубают метал з іншого боку або з усіх чотирьох сторін, після чого відламують отрубаемую частина. Для прискорення і спрощення рубання застосовують допоміжний інструмент - нижиик (підсікання). Підсічку хвостовиком вставляють в квадратне отвір ковадла, потім заготовку кладуть на підсічку, а зверху встановлюють ковальське зубило, як показано на 10, Д і наносять кувалдою удари по зубилу. Таким чином відбувається одночасна рубка металу з двох сторін зубилом і підсічкою.
Чавунні труби перерубують зубилом на дерев'яних підкладках. Спочатку по колу труби крейдою намічають лінію переруби, а потім, підклавши під трубу підкладки, за два-три проходи надрубают трубу зубилом по лінії розмітки (І, а), поступово повертаючи її. Перевіривши глибину прорубаної канавки, яка повинна становити не менше товщини стінки 7з труби, легкими ударами молотка відокремлюють частину труби. Зубило при роботі потрібно тримати перпендикулярно до осі труби (11, б). Торець труби в місці переруби повинен бути рівним, перпендикулярним до осі труби і збігатися з наміченої лінією переруби. Правильність Торця перевіряють на око, а контролюють косинцем.
§ 3. Механізми та пристрої для рубання металу
Більш продуктивною є механізована рубка металу пневматичним молотком (12),працюючим під дією стисненого повітря тиском 5 - 6 кгс/см2. Стисле повітря підводиться до молотка по шлангах від компресора. Пневматичний молоток складається з циліндра /), який вставляють зубило, поршня, що рухається в циліндрі, і повітророзподільного пристрою. Завдяки воздухораспределительному пристрою поршень отримує поступальний і зворотний рух і швидко переміщається вперед і назад по циліндру. При поступальному русі поршень вдаряє по зубилу, яке розрубує метал. Молоток включають в роботу натисканням курка 6. Робочий тримає молоток двома руками і направляє на зубило місце рубки.
Змін. |
Арк. |
№ докум. |
Підпис |
Дата |
Арк. |
Ножі кріпляться до обойм болтами. Внутрішні діаметри лез ножів повинні бути на 2 мм менше зовнішніх діаметрів перерубаемых труб. Для кожного діаметра труб є пара ножів і пара ковзанок, що встановлюються на швелері для подачі труб до ножів.
На пресі працюють наступним чином. Спочатку встановлюють ножі і катки відповідно з діаметром перерубаемых труб. Піднявши маховиком верхню обойму з ножем, укладають трубу на катки так, щоб лінія переруби збіглася з вістрям нижнього ножа. Потім різким ривком повертають маховик у зворотний бік, опускаючи при цьому ходовий гвинт з верхнім ножем. Від різкого натиску нижнього і верхнього ножів на бічних сторонах труби спочатку з'являється надріз, труба расклинивается і потім розколюється са дві частини. Прес обслуговує один робітник.
Механізм ВМС-36А (14) для перерубки чавунних каналізаційних труб діаметром 50 і 100 мм працює за принципом приводного преса. На зварний станині / механізму змонтований редуктор з двома головками 2. Одна головка призначена для перерубки труб діаметром 50 мм, друга-для труб діаметром 100 мм. Труби перерубаются чотирма рухомими ножами, вмонтованими в патрони головок механізму. Механізм включається в роботу від електродвигуна потужністю 1,5 кВт, частотою обертання 1420 об/хв. Запуск двигуна здійснюється ножною педаллю.
Для перерубки труб спочатку включають електродвигун. Потім
беруть заздалегідь розмічену трубу і укладають її на опори так, щоб лінія розмітки на трубі збіглася з лезом ножа. Після цього ногою натискають на педаль. Ножі опускаються на трубу, яка від натиску ножів перерубав по лінії розмітки. Після перерубки ножі повертаються в початкове положення і робота головки автоматично припиняється. Час перерубки труб одного циклу становить 3 с. Кожен з чотирьох ножів охоплює перерубаемую трубу на довжині, що дорівнює чверті її окружності. На 15 показано площині різальних ножів, геометрія яких враховує особливості перерубаемого матеріалу, тобто крихкість
Змін. |
Арк. |
№ докум. |
Підпис |
Дата |
Арк. |
При зближенні ножі в перший момент стосуються труби у восьми точках. При подальшому зближенні вони врізаються в трубу; утворюються лунки, розташовуються по колу. Близько лунок виникають мікротріщини, спрямовані від лунки до лунки і в глиб металу. В ході процесу мікротріщини і зливаються утворюються біжать тріщини того ж напрямку, які випереджають подачу ножів. Це призводить до того, що один кінець труби відокремлюється від іншого.
Ножами описаної конструкції можна відрізати від чавунних каналізаційних труб кільця довжиною 20 мм.
При рубці щоб уникнути ударів і поранень необхідно дотримуватися наступних заходів безпеки:
міцно насаджувати молоток або кувалду на ручку;
надійно зміцнювати метал в лещатах і при рубці на ковадлі підтримувати отрубаемую частину заготовки;
застосовувати захисні сітки при рубці твердого або крихкого металу, щоб відлітають осколки не поранили працюючого або знаходиться поблизу людини;
працювати справним інструментом і на справних верстатах;
при перерубке труб на пресі працювати в рукавицях.
До перерубки труб необхідно перевірити справність механізму, електрообладнання і захисних огороджень.
ПРАКТИЧНА РОБОТА №4
Змін |
Арк. |
№ документа |
Підпис |
Дата |
Аркуш |
Розробив |
Перевірив |
Н. Контр. |
Затвердив |
Літера |
Аркушів |
Різання – відділення частин заготовок від сортового або листового металу. Різання виконують як зі зняттям стружки, так і без зняття. Різання зі зняттям стружки здійснюють ручною ножівкою, на ножівкових, кругло пиляльних, токарно-відрізних верстатах, а може бути газове, дугове тощо. Без зняття стружки матеріали розрізують ручними важільними і механічними ножицями, гострозубцями, труборізами, прес-ножицями у штампах. До різання належить також надрізування металу.Суть процесу різання ножицями полягає у відокремленні частини металу під дією пари різальних ножів, які виготовляють зі сталі У7, У8; бокові поверхні лез загартовані до S2 .58 НRCе, відшліфовані та загострені.Звичайні ручні ножиці застосовують для різання стальних листів завтовшки 0,5 .1 мм і листів з кольорових металів завтовшки до 1,5 мм. Їх виготовляють з прямими і кривими різальними лезами.За розміщенням різальної кромки лез ручні ножиці поділяють на праві та ліві.Ліві – ножиці, у яких на різальній частині кожної половини скіс розташовано з лівого боку. Ними ріжуть по правій кромці виробу проти годинникової стрілки. Праві – ножиці у яких скіс на різальній частині кожної половини знаходиться з правого боку. Ними ріжуть по лівій кромці виробу у напрямі за годинниковою стрілкою.(мал. 110).Річні малогабаритні силові ножиці (мал. 113) служать для різання листового металу завтовшки до 2,5 мм і прутків двометром до 0,8 мм. Робоча рукоятка складається з двох послідовно з’єднаних важелів. Перший важіль на одному плечі якого закріплено ніж з’єднаний за допомогою гвинта з рукояткою, ножі ножиць змішані й прикріплені до важелів потайними заклепками.
Різання ножівкою
Ножівка – інструмент для різання листів штабового круглого та профільного металу, а також для прорізування шліців, пазів, обрізування й вирішування заготовок по контуру та інших робіт. Ручна ножівка складається з рамки та ножівкового полотна. На одному кінці рамки є нерухома головка з хвостовиком і рукояткою, а на іншому гвинтом і гайкою для натягування полотна. У головках є прорізи у які встановлюють ножівкове полотно закріплюють шурупами. Рамки для ножівок виготовляють або суцільними для ножівкового полотна однієї певної довжини або розсувними, що дає змогу закріплювати ножівкове полотно різної довжини. Ножівкове полотно – тонка, вузька стальна пластина з двома отворами для закріплення, яка має зуби на одному з ребер. Їх виготовляють зі сталі У10А та Х6ВоР їх твердість 61 .64 НРСе.
Змін |
Арк. |
№ документа |
Підпис |
Дата |
Аркуш |
Розробив |
Перевірив |
Н. Контр. |
Затвердив |
Літера |
Аркушів |
Обпилювання металу
Обпилюванням називається операція по обробці металів і інших матеріалів зняттям невеликого шару напилками вручну або на обпилювальних верстатах.
За допомогою напилка слюсар додає деталям необхідну форму і розміри, проводить припасування деталей один до одного, підготовлює кромки деталей під зварювання і виконує інші роботи.
За допомогою напилків обробляють площини, криволінійні поверхні, пази, канавки, отвори будь-якої форми, поверхні, розташовані під різними кутами, і т. п. Припуски на обпилювання залишаються невеликими від 0,5 до 0,025 мм. Точність обробки обпилюванням від 0,2 до 0,05 мм, в окремих випадках до 0,001 мм. ручна обробка напилком в даний час значною мірою замінена обпилюванням на спеціальних верстатах, але повністю ручне обпилювання ці верстати витіснити не можуть, оскільки пригоночні роботи при збиранні і монтажі обладнання часто доводиться виконувати вручну.
Напилок являє собою стальний брусок певного профілю і довжини, на поверхні якого є насічки (нарізки), створюючи западини і гостро заточені зубці, що мають в перетині форму клина. Напилки виготовляють з сталі У10А або У13А (відпускається легована хромиста сталь ШХ15 або 13Х), після насічення піддають термічній обробці.
Напилки поділяють: по розміру насічки, за формою насічки, по довжині і формі бруска, за призначенням.
Види і основні елементи насічок. Насічки на поверхні напилка утворять зубці, які знімають стружку з матеріалу, що обробляється.
Чим менше насічок на 1 см довжини напилка, тим крупніше зуб. Розрізнюють напилки з одинарною, тобто простою насічкою , з подвійною, або перехресною, крапкової, також є з рашпільної , і дуговий.
Напилки з одинарною насічкою можуть знімати широку стружку, рівну довжині всієї насічки. Їх застосовують при обпилюванні м'яких металів (латуні, цинку, бабіту, свинцю, алюмінію, бронзи, міді і з незначним опором різанню, а також неметалічних матеріалів. Крім того, ці напилки використовуються для заточування пилок, ножів, а також для обробки дерева і пробки.
Напилки з подвійною (т. е. перехресної) насічкою застосовують для обпилювання сталі, чавуна і інших твердих матеріалів з великим опором різанню.
Змін. |
Арк. |
№ докум. |
Підпис |
Дата |
Арк. |
Тип напилка визначається формою поверхні, що обробляється, довжина розмірами її. Напилок беруть довжиною на 150 мм більше розміру поверхні, що обробляється. Для обпилювання тонких пластин, пригоночних і довідних робіт беруть короткі напилки з дрібною насічкою. Коли потрібно зняти великий припуск, працюють напилками довжиною 300...400 мм з великою насічкою. Номер насічки вибирають в залежності від вигляду обробки і розмірів припуску. Для чорнової обробки застосовують напилки з насічкою № 0 і 1. Вони знімають припуск до 1 мм. Точність обробки цими напилками невисока 0,1 0,2 мм. Чистову обробку виконують напилками з насічкою № 2. На обробку особистими напилками залишають припуск до 0,3 мм. Ними забезпечується точність 0,02 0,005 мм. Для остаточного обпилювання і доведення поверхні з точністю до 0,001 мм беруть напилки № 3, 4 і 5. Вони знімають шар металу до 0,01 0,02 мм.
Тонкі заготівлі з сталі підвищеної твердості рекомендується обпилювати напилками з насічкою № 2. При відсутності спеціальних напилків кольорові метали обробляють напилками загального призначення з насічкою № 1.
Існують такі види напилків як:
Чорновий – для чорнової обробки металу, має дуже крупну насічку;
Чистовий – для чистової обробки металу, має середню насічку;
Надфіль – напилок малої площі перерізу який використовуються для обробки дрібних деталей та чистової обробки;
Бархатний – використовується для кінцевої обробки металу, має дуже дрібну насічку.
Всі ці напилки також поділяються за формою перерізу: плоскі, круглі, квадратні, трикутні, напівкруглі, ромбічні.
Підготовка поверхні до обпилювання. Заготовку очищають металевими щітками від бруду, масла, окалини, ливарну кірку зрубують зубилом, видаляють наждаком або старим напилком.
Закріплення заготівлі. Заготовку, що обробляється затискають в лещатах обпилюваною площиною горизонтально, на 8-10 мм вище за рівень губок. Заготовку з обробленими поверхнями закріпляють, надівши на губки нагубники з м'якого матеріалу (мідь, латунь, алюміній, м'яка сталь).
Прийоми обпилювання.
Положення корпусу вважається правильним, якщо права рука з напилком, встановленим на губках лещат (початкове положення), зігнена в лікті, утворить кут 90° між плечовою і ліктьовою частиною руки. При цьому корпус працюючого повинен бути прямим і розгорненим під кутом 45° до лінії осі лещат.
Положення ніг. При початку робочого ходу напилка маса тіла доводиться
Змін. |
Арк. |
№ докум. |
Підпис |
Дата |
Арк. |
При робочому ході напилка (від себе) основне навантаження доводиться на ліву ногу, а при зворотному (холостому) ході на праву, тому м'язи ніг навперемінно відпочивають.
При знятті напилком товстих шарів металу доводиться натискати на напилок з великою силою, тому праву ногу відставляють від лівої назад на півкроку і вона в цьому випадку є основною опорою. Ці роботи, як точні, частіше виконують сидячи.
Положення рук (хватка напилка) має надзвичайно важливе значення. Слюсар бере в праву руку напилок за ручку так, щоб ручка упиралася в долоню руки, чотири пальці захоплювали ручку знизу, а великий палець вміщувався зверху. Долоню лівої руки накладають декілька упоперек напилка на відстані 20 - 30 мм від його кінця. При цьому пальці повинні бути злегка зігнені, але не звисати; вони не підтримують, а тільки притискують напилок. Лікоть лівої руки повинен бути трохи підведений. Права рука від ліктя до кисті повинна складати з напилком пряму лінію.
Координація зусиль. При обпилюванні повинна дотримуватися координація зусиль натиску (балансировка), що полягає в правильному збільшенні натиску правої руки на напилок під час робочого ходу при одночасному зменшенні натиску лівої руки. Рух напилка повинен бути горизонтальним, тому натиски на ручку і кінець напилка повинні змінюватися. Розподіл зусиль натиску при обпилюванні залежить від положення точки опори напилка на поверхні, що обробляється. При робочому русі напилка натиск лівою рукою поступово зменшують. Регулюючи натиски на напилок, домагаються отримання рівної обпилюваної поверхні без завалів по краях.
У разі ослаблення натиску правої руки і посилення лівою може статися завал поверхні уперед. При посиленні натиску правої руки і ослабленні лівої руки вийде завал назад.
Притискувати напилок до поверхні, що обробляється необхідно при робочому ході (від себе). При зворотному ході не треба відривати напилок від поверхні деталі. Під час зворотного ходу напилок повинен лише ковзати. Чим грубіше обробка, тим більше повинне бути зусилля на робочому ході.
При чистовому обпилюванні натиск на напилок повинен бути значно менше, ніж при чорновому. У цьому випадку лівою рукою натискають на носок напилка не долонею, а лише великим пальцем.
Види обпилювання
Обпилювання поверхонь є складним процесом. Частіше всього дефектом при обпилюванні поверхонь є неплощинність. Працюючи напилком в
Змін. |
Арк. |
№ докум. |
Підпис |
Дата |
Арк. |
Спочатку обпилювання виконують зліва направо під кутом 30 - 40° до осі лещат, потім, не перериваючи роботи, прямим штрихом і закінчують обпилювання косим штрихом під тим же кутом, але праворуч наліво. Така зміна напряму руху напилка забезпечує отримання необхідної площинності і шорсткості поверхні.
Контроль обпиляної поверхні.
Для контролю обпиляних поверхонь користуються перевірочними лінійками, штангенциркулями, косинцями і перевірочними плитами. Перевірочну лінійку вибирають в залежності від довжини поверхні, що перевіряється, тобто перевірочна лінійка по довжині повинна перекривати поверхню, що перевіряється.
Перевірку якості обпилювання поверхні перевірочною лінійкою проводять на просвіт. Для цього деталь звільняють від лещат і підіймають на рівень очей; перевірочну лінійку беруть правою рукою за середину і прикладають ребро перевірочної лінійки поверхні, що перпендикулярно перевіряється.
Для перевірки поверхні у всіх напрямах спочатку лінійку ставлять по довгій стороні в двох-трьох, потім по короткій також в двох-трьох місцях і, нарешті, по одній і іншій діагоналях. Якщо просвіт між лінійкою і поверхнею, що перевіряється вузький і рівномірний, означає площина оброблена задовільно.
У тих випадках, коли поверхня повинна бути обпиляна особливо ретельно, перевірка точності обпилювання проводиться за допомогою перевірочної плити на фарбу. У цьому випадку на робочу поверхню перевірочної плити за допомогою тампона (згорненої ганчірки) наноситься тонкий рівномірний шар фарби (синька, сажа або сурик, розведений в маслі). Потім перевірочну плиту накладають на поверхню (якщо деталь громіздка), що перевіряється, роблять декілька кругових рухів, після цього плиту знімають.
Змін |
Арк. |
№ документа |
Підпис |
Дата |
Аркуш |
Розробив |
Перевірив |
Н. Контр. |
Затвердив |
Літера |
Аркушів |
ПРАКТИЧНА РОБОТА №6
Обпилювання заготовок
У практиці слюсарної обробки найчастіше зустрічаються такі види обпилювання:обпилювання плоских— спряжених, паралельних і перпендикулярних поверхонь деталей; обпилювання криволінійних поверхонь; обпилювання циліндричних і конічних деталей з припасуванням їх по місцю.
Обпилювання починається, як правило, з перевірки припуску на обробку, який міг би забезпечити виготовлення деталі за розмірами, вказаними на кресленні. Перевіривши розміри заготовки, визначають базу, тобто поверхню, від якої слід додержувати розміри деталі і взаємне розміщення її поверхні.
Розмір напилка виби рають з таким розрахунком, щоб він був довший від обпилюваної поверхні не менше ніж на 150 мм. Якщо клас чистоти поверхні на кресленні не вказаний, обпилювання провадять лише драчовим напилком. При необхідності одержати більш чисті і гладенькі поверхні обпилювання закінчують личкувальним напилком. Продуктивність праці під час обпилювання залежить від послідовності переходів, правильного користування напилком, а також від застосовуваних під час обпилювання пристроїв для закріплення деталі і напряму напилка.
Змін. |
Арк. |
№ докум. |
Підпис |
Дата |
Арк. |
Розглянемо послідовність переходів під час обпилювання широких площин — боків плоско-паралельної прямокутної плитки (рис. 134).
Перед початком обпилювання деталь затискують у лещатах так, щоб оброблювана поверхня була розміщена горизонтально і виступала на 5—8 мм над губками лещат. Обробку починають з широкої площини 1 (рис. 134, а), прийнятої за основну вимірювальну базу. Чорнове обпилювання ведуть плоским драчовим напилком, а чис- тове — плоским личкувальним напилком. Закінчивши обпилювання площини, деталь знімають. Перевірку правильності площини провадять лінійкою, накладаючи її вздовж, впоперек і по діагоналі обробленої поверхні. Потім переходять до обпилювання таким самим способом Другої широкої площини 2. При цьому паралельність площин 1 і 2 контролюють кронциркулем. Установивши на лещатах нагубники, обпилюють одну з вузьких площин (ребро 3) і перевіряють її лінійкою і кутником від площини 1 (рис. 134,6). Потім провадять обпилювання ребер 4, 5 і 6 (рис. 134, а) з перевіркою їх від базової площини 1 і першого ребра 4 (рис. 134, в).
Обпилювання вузьких площин на тонких деталях становить значні труднощі. Дрібні і тонкі деталі (завтовшки до 4 мм) важко рівномірно затиснути в лещатах, щоб одержати під час обпилювання рівну площину. З метою підвищення продуктивності під час виконання цієї роботи застосовують склепування 3—10 таких деталей у пакети. Прийоми обпилювання ребер у такому пакеті не відрізняються від обпилювання плитки з широкими ребрами.
Змін. |
Арк. |
№ докум. |
Підпис |
Дата |
Арк. |
Обпилювальна призма складається з корпуса 1 (рис. 135, а), на бічній поверхні якого жорстко закріплюються притискач 2, кутник 3 і лінійка 4. Кутник або лінійка використовуються для правильного встановлювання оброблюваної деталі, а притискач — для її закріплення. Поверхня А корпуса призми є напрямною для напилка. Шар металу заготовки, що підлягає зніманню, повинен виступати над площиною А корпуса призми. Корпус обпилювальної призми закріплюють в слюсарних лещатах у горизонтальному положенні.
У практиці обпилювання тонких деталей застосовуються також намітники-рамки (рис. 135,6). Обпилювання в такому пристрої виключає «завали», оскільки деталь затискується не збоку пристрою, а в середині — в проймі. Розмічену заготовку вставляють у рамку, трохи притискуючи її гвинтом до внутрішньої стінки рамки. Уточнюють встановлення, добиваючись збігання риски на заготовці з внутрішнім ребром рамки, після чого остаточно закріплюють гвинти. Рамку затискують у лещатах і обпилюють вузьку поверхню заготовки до рівня робочої кромки рамки.
Змін. |
Арк. |
№ докум. |
Підпис |
Дата |
Арк. |
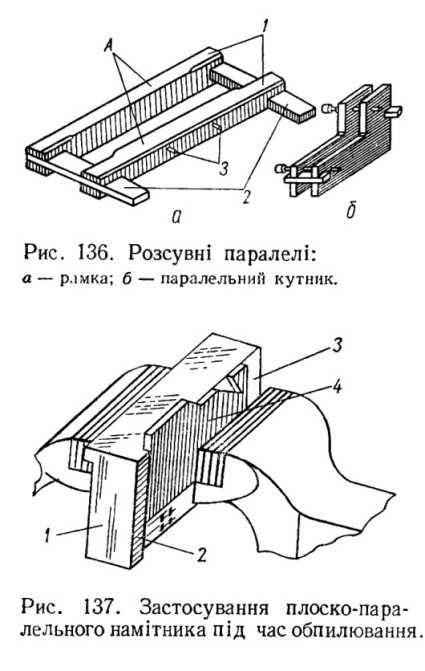
Розсувну рамку слід встановлювати в лещата так, щоб вона спиралась на губки лещат двома парами штифтів . Для обпилювання заготовок під прямим кутом користуються розсувним паралельним кутником (рис. 136,6). Плоскопаралельний намітник являє собою загартовану пластину з двома Г-подібними виступами 1 і 2 (рис. 137). На такому намітнику можна обпиляти чотири боки (кромки) заготовки під кутом 90°, не контролюючи правильності кутів у процесі роботи. Під час установлювання намітник повинен лягти виступом 1 на нерухому губку. Потім розміщують оброблювану тонку заготовку 4 між рухомою губкою лещат і площиною 3 намітника, упираючи її ребро у виступ 2. Трохи затиснувши лещата, легким постукуванням по заготовці суміщують нанесену на ній розмічальну риску з верхньою кромкою намітника. Після цього остаточно затискують заготовку в лещатах і починають обпилювання під кутом 25—ЗО® до бічних сторін лещат (заготовки). Якщо робота провадиться дра- човим напилком, то, не доходячи 0,3 мм до верхньої поверхні на- мітника, його відкладають і продовжують обпилювання личкувальним напилком і працюють ним доти, поки кромка заготовки не зрівняється з верхньою поверхнею намітника.
Змін. |
Арк. |
№ докум. |
Підпис |
Дата |
Арк. |

Змін |
Арк. |
№ документа |
Підпис |
Дата |
Аркуш |
Розробив |
Перевірив |
Н. Контр. |
Затвердив |
Літера |
Аркушів |
Свердлування отворів
Свердління є одним з найпоширеніших методів одержання отвору різанням. Різальним інструментом тут є свердло, яке дає можливість як одержувати отвір у суцільному
матеріалі (свердління), так і збільшувати діаметр уже просвердленого отвору (розсвердлювання).
Під час свердління оброблювану деталь закріплюють на столі свердлильного верстата прихватами, у лещатах, на призмах і т. п., а зверху надають двох сумісних рухів (рис. 152) — обертального за стрілкою V і поступального (направлений вздовж осі свердла) за стрілкою 5. Обертальний рух свердла називається головним (робочим) рухом. Поступальний рух вздовж осі свердла називається р у- хом подачі.
Свердла для глибокого свердління застосовуються на спеціальних верстатах для одержання точних отворів Рис. 152. Робота свердла малого діаметра. Під глибоким свердлін- під час свердління.ням звичайно розуміють свердління отво
рів, довжина яких перевищує їх діаметр у 5 раз і більше. Центрові свердла (рис. 153,г) застосовуються для одержання центрових заглиблень на оброблюваних деталях.
Свердління застосовується під час виконання багатьох слюсарних робіт. Воно виконується на приводних свердлильних верстатах і вручну — ручними дрилями, з допомогою механізованого інструменту — електричними і пневматичними
дрилями, а також електроіскровим і ультразвуковим методами.
Свердла, їх конструкції і призначення. Зд конструкцією і призначенням свердла поділяються на ряд видів.
Змін. |
Арк. |
№ докум. |
Підпис |
Дата |
Арк. |
Спіральні свердла з циліндричними і конічними хвостовиками (рис. 153,6, в) використовуються як для ручного свердління, так і для роботи на верстатах (свердлильних, револьверних і ін.).
Свердла для глибокого свердління застосовуються на спеціальних верстатах для одержання точних отворів малого діаметра. Під глибоким свердлінням звичайно розуміють свердління отворів, довжина яких перевищує їх діаметр у 5 раз і більше.
Центрові свердла (рис. 153, г) застосовуються для одержання центрових заглиблень на оброблюваних деталях.
Комбіновані свердла дають можливість провадити одночасну обробку одноосьових отворів (рис. 153,5), а також одночасне свердління і зенкування або розвірчування отворів (див., наприклад, рис. 153,е).
Для виготовлення свердел, як правило, застосовують такі інструментальні матеріали: вуглецеву інструментальну сталь марок У10А і У12А, леговані сталі — хромисту марки X і хромокрем- нисту 9ХС; швидкорізальну сталь марок Р9 і Р18. В останні роки для цієї мети застосовують також металокерамічні тверді сплави марок ВК6, ВК8 і Т15К6.
Свердла з швидкорізальних сталей виготовляють зварними: робочу частину — з швидкорізальної сталі, а решту — з менш дорогої конструкційної сталі. Найпоширенішими є спіральні свердла з швидкорізальних сталей.
Змін. |
Арк. |
№ докум. |
Підпис |
Дата |
Арк. |
Різальна частина, на якій розміщені всі різальні елементи свердла, складається: з двох зуб’їв (пер), утворених двома спіральними канавками для відведення стружки (рис. 154,6); перемички (серцевини) — середньої частини свердла, що з’єднує обидва зуби (пера); двох передніх поверхонь, по яких збігає стружка, і двох задніх поверхонь; двох стрічечок, призначених для направлення свердла, калібрування отвору і зменшення тертя свердла об стінки отвору; двох головних різальних кромок, утворених перетином передніх і задніх поверхонь і виконуючих основну роботу різання; поперечної кромки (перемички), утвореної перетином обох задніх поверхонь. На зовнішній поверхні свердла між краєм стрічечки і канавкою розташована трохи заглиблена частина, що йде по гвинтовій лінії, яка називається спинкою зуба.
Зменшення тертя свердла об стінки просвердлюваного отвору досягається також тим, що робоча частина свердла має зворотний конус, тобто діаметр свердла біля різальної частини більший, ніж на другому кінці, біля хвостовика. Різниця між величиною цих діаметрів становить 0,03—0,12 мм на кожні 100 мм довжини свердла.
У свердел, оснащених пластинками твердих сплавів, зворотна конусність приймається від 0,1 до 0,3 мм на кожні 100 мм довжини.
Змін. |
Арк. |
№ докум. |
Підпис |
Дата |
Арк. |
Кут при вершині свердла 2ср розміщений між головними різальними кромками. Він дуже впливає на роботу свердла. Величина цього кута вибирається залежно від твердості оброблюваного матеріалу і коливається в межах від 80 до 140°;для сталей, чавунів і твердих бронз 2ср = 116-И18°; для латуней і м’яких бронз 2ф = 130°; для легких сплавів — дуралюміну, силуміну, електрону і бабіту 2ф = 140°; для червоної міді 2ф = 125°; для ебоніту і целулоїду 2ф = 80-т-90°.
Для підвищення стійкості свердел діаметром 12 мм і більше застосовують подвійну заточку свердел; при цьому головні різальні кромки мають форму не прямої, як при звичайному заточуванні (рис. 155,а), а ламаної лінії (рис. 155,6). Основний кут 2ф = 116-і- -т-1180 (для сталей і чавунів), а другий кут 2ф0= 70-г-75°.
свердло (особливо малого діаметра) із збільшенням кута нахилу гвинтової канавки ослаблюється. Тому у свердел малого діаметра цей кут роблять меншим, ніж у свердел великого діаметра.
Кут нахилу гвинтової ка-
навки повинен вибиратися залежно від властивостей об- j$ роблюваного металу. Для обробки, наприклад, червоної Рис. 155. Геометричні параметри спіраль-
Кут нахилу гвинтової канавки позначається буквою омега о> (рис. 155,а). Із збільшенням цього кута процес різання полегшується, поліпшується вихід стружки. Але
міді і алюмінію цей кут тре
ба брати в межах 35—40°, а для обробки сталі ш = 25° і менше.
Змін. |
Арк. |
№ докум. |
Підпис |
Дата |
Арк. |
Передній кут ^ (гамма) у різних точках різальної кромки має різну величину: він більший біля периферії свердла і помітно менший біля його осі. Так, якщо біля зовнішнього діаметра передній кут y = 25-КЗО®, то біля перемички він близький до 0°. Непостійність величини переднього кута відноситься до недоліків спірального свердла і є однією з причин нерівномірного і швидкого його спрацювання.
Задній кут свердла а (альфа) передбачений для зменшення тертя задньої поверхні об поверхню різання. Цей кут розглядається в площині А—А, паралельній осі свердла (рис. 155,в). Величина заднього кута також змінюється в напрямі від периферії до центра свердла; біля периферії він дорівнює 8—12°, а біля осі а = 2(Н-26°.
Кут нахилу поперечної кромки ф (псі) для свердел діаметром від 1 до 12 мм коливається від 47 до 50° (рис. 155,в), а для свердел діаметром понад 12 мм ф =55°.
Свердла, оснащені пластинками твердих сплавів, порівняно з свердлами, виготовленими з сталей, мають меншу довжину робочої частини, більший діаметр серцевини і менший кут нахилу гвинтової канавки. Ці свердла мають високу стійкість і забезпечують більш високу продуктивність. Особливо ефективне застосування свердел з пластинками твердих сплавів під час свердління і розсвердлювання чавуну, твердої сталі, пластмас, скла, мармуру та інших твердих матеріалів.
Свердла, оснащені пластинками твердих сплавів, випускаються чотирьох типів: спіральні з циліндричним хвостовиком (рис. 156,а); спіральні з конічним хвостовиком (рис. 156,6); з прямими канавками і конічним хвостовиком (рис. 156,б) і з косими канавками і циліндричним хвостовиком (рис. 156,2).
Процес різання під час свердління. У процесі свердління під діянням сили різання різальні поверхні свердла стискують частинки металу, що до них прилягають, і коли тиск, створюваний свердлом, перевищить сили зчеплення частинок металу, починають утворюватись елементи стружки, і вона відділяється.
Змін. |
Арк. |
№ докум. |
Підпис |
Дата |
Арк. |
У процесі свердління розрізняють такі елементи різання: швидкість різання, глибина різання, подача, товщина і ширина стружки (рис. 157).
Головний робочий рух свердла (обертальний) характеризується швидкістю різання.
Швидкість різання — це шлях, що проходить у напрямі головного руху найбільш віддалена від осі інструмента точка різальної кромки за одиницю часу. Прийнято швидкість різання позначати латинською буквою V і вимірювати в метрах за хвилину.
ПРАКТИЧНА РОБОТА №8
Зенкування та розгортання отворів
Зенкуванням називається обробка вхідної або вихідної частини отвору для знімання фасок, задирок, а також утворення заглиблень під головки^ болтів, гвинтів і заклепок.