Подготовка изделия под сварку.
Изм. |
Лист |
№ докум. |
Подпись |
Дата |
Лист |
15.01.05. 000 ПЗ |
а) Метал правят и зачищают с целью устранения загрязнения и неровностей образованных при транспортировки и хранении.
б) Затем выполняют разметку путем переноса размеров на заготовку с чертежа на метал.
в) Затем выполняем резку на ножницах, автоматическими машинами, резаками либо сжатой дугой.
г) Обрабатываем кромки, устраняя неровности с помощью напильника.
д)При необходимости использовать холодную гибку металла или в нагретом состоянии.
е) В зависимости от толщины металла и формы разделки кромок подготавливают обрезкой ножницами, рубкой, газовой резкой, кислородной резкой обеспечивающий высокую производительность и точность подготовки кромок.
х) Основной метал до сварки в местах сборки должен быть очищен от ржавчины, масла, влаги и других загрязнений которые могут привести к дефекту в шве.
з) Перед сваркой прожигают место сварки газовым пламенем или продувают сжатым воздухом.
и) Если толщина металла до 4 мм то разделка кромок не делается если толщена металла более 4 мм то выполняется разделка кромок.
Изм. |
Лист |
№ докум. |
Подпись |
Дата |
Лист |
15.01.05. 000 ПЗ |
1) V=3 m3 V=S*H H= 1m
2) S= j/h= 3/1 = 3 m3
3) S= ПR2
4) R= s/п= 3/3.14= 0.97 Д= 0.97*2= 1.94
5) Lокр=П*Д=3.14*1.94= 6.09м= 6090мм
6) N=L/300= 6090/300=20 прихваток
4)
Изм. |
Лист |
№ докум. |
Подпись |
Дата |
Лист |
15.01.05. 000 ПЗ |
Во время сварки электросварщик сообщает концу электрода движение в трех направлениях
Первое движение — поступательное, по направлению оси электрода для поддержания необходимой длины дуги lд, которая должна быть lд = (0,5 + 1,1)dэ, где dэ — диаметр электрода, мм Длина дуги оказывает большое влияние на качество сварного шва и его форму. Длинной дуге соответствует интенсивное окисление и азотирование расплавленно го металла и
повышенное его разбрызгивание. При сварке электродами фтористо-кальциевого типа увеличение длины дуги приводит к пористости металла шва.
Второе движение — вдоль оси валика, для образования сварного шва. Скорость движения электрода зависит от величины тока, диаметра электрода, типа и пространственного положения шва. Правильно выбранная скорость перемещения электрода вдоль оси шва обеспечивает требуемую форму и качество сварного шва. При большой скорости перемещения электрода основной металл не успевает проплавиться, вследствие чего образуется недостаточная глубина проплавления — непровар. Недостаточная скорость перемещения электрода приводит к перегреву и прожогу (сквозное проплавление) металла, а также снижает качество и производительность сварки. Правильно выбранная скорость продольного движения электрода вдоль оси шва позволяет получить его ширину на 2 — 3 мм больше, чем диаметр электрода.
Сварной шов, образованный в результате первого и второго движений электрода, называют ниточным. Его применяют при сварке металла небольшой толщины, при наплавочных работах и при подварке подрезов.
Третье движение — колебание концом электрода поперек шва, для образования уширенного валика, который применяется чаще, чем ниточный. Для образования уширенного валика электроду сообщают поперечные колебательные движения, чаще всего с постоянной частотой и амплитудой, совмещенные с поступательным движением электрода вдоль оси шва и оси электрода. Поперечные колебательные движения электрода разнообразны и определяются формой, размерами, положениями шва в пространстве и навыком сварщика. На рис. 40 показаны поперечные колебания, описываемые концом электрода.
Изм. |
Лист |
№ докум. |
Подпись |
Дата |
Лист |
15.01.05. 000 ПЗ |
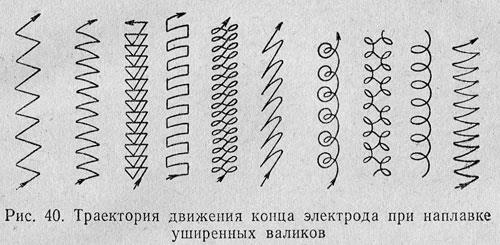
Траектория движения конца электрода при наплавке уширенных валиков
Существует два способа зажигания дуги покрытыми электродами – прямым отрывом и отрывом по кривой. Первый способ называют зажиганием впритык. Второй напоминает движение при зажигании спички и поэтому его называют чирканьем.
Немедленно после зажигания дуги начинается плавление основного и электродного металлов. На изделии образуется ванна расплавленного металла. Сварщик должен подавать электрод в дугу со скоростью, равной скорости плавления электрода. Нормальной считают длину дуги, равную 0,5-1,1 диаметра стержня электрода.
Увеличение длины дуги снижает устойчивое ее горение, глубину проплавления основного металла, повышает потери на угар и разбрызгивание электрода, вызывает образование шва с неровной
поверхностью и усиливает вредное воздействие окружающей атмосферы на расплавленный металл.
Наклон электрода при сварке зависит от положения сварщика в пространстве, толщины и состава свариваемого металла, диаметра электрода, вида и толщины покрытия.
Для получения плотного и ровного шва при сварке в нижнем положении на горизонтальной плоскости угол наклона электрода должен быть 15° от вертикали в сторону ведения шва.Для получения валика нужной ширины производят поперечные колебательные движения электрода. Чаще всего применяют швы шириной от 1,5 до 4 диаметров электрода, полученные с помощью поперечных колебательных движений электрода.
Сварка швов в вертикальном положении. При ручной сварке в вертикальном положении стекание расплавленного металла также оказывает существенное влияние на формирование шва и глубину проплавления. Вертикальные швы обычно выполняют на подъем. В этом случае удается обеспечивать требуемый провар и поддерживать расплавленный металл на кромках. Однако производительность сварки низкая и увеличивается при сварке на спуск. Однако из-за малой глубины проплавления это
Изм. |
Лист |
№ докум. |
Подпись |
Дата |
Лист |
15.01.05. 000 ПЗ |
Особенно неблагоприятные условия формирования шва наблюдаются при выполнении на вертикальной плоскости горизонтальных швов, так как расплавленный металл натекает на нижнюю свариваемую деталь.
Сварка швов в потолочном положении. Достаточно сложна и ручная сварка в потолочном положении. Расплавленный металл в сварочной ванне в этом случае удерживается от вытекания силой поверхностного натяжения.
Поэтому необходимо, чтобы вес расплавленного металла не превысил эту силу. Для этого стремятся уменьшить размеры сварочной ванны, выполняя сварку периодическими короткими замыканиями, давая возможность металлу шва частично закристаллизоваться. Применяют также уменьшенные диаметры электродов, снижают силу сварочного тока, используют специальные электроды, обеспечивающие получение вязкой сварочной ванны.
Сварка швов в горизонтальном положении. При сварке горизонтальных соединений подготовка кромок необходима только для верхней кромки. Дугу возбуждают вначале на нижней горизонтальной кромке, а затем перемещают на скошенную кромку. Горизонтальные швы выполняют вертикально расположенным электродом, углом назад и углом вперед. Движение электрода можно осуществлять на себя и от себя. Угол наклона электрода к вертикальной плоскости свариваемого изделия должен составлять 75 - 80°.При сварке в нижнем положении расплавленный металл не может вытечь из ванны,
Изм. |
Лист |
№ докум. |
Подпись |
Дата |
Лист |
15.01.05. 000 ПЗ |
Сварка стыковых бесскосных швов. При обычных приемах сварка бесскосных швов применяется для толщины металла до 6—8 мм
При сварке стыковых бесскосных швов необходимо обеспечить провар на всю толщину листа.
Валик наплавляется вдоль кромок при небольшом колебании электрода в поперечном направлении. Если сварка осуществляется электродом диаметром 6 мм, то ширина валика получается достаточной без поперечных колебательных движений электрода. При сварке стыковых бесскосных швов внимание сварщика должно быть обращено на наличие зазора между кромками и их равномерное расплавление.
Для получения шва высокой прочности без непровара в нижней части кромок следует, если позволяет конструкция, делать подварку с обратной стороны . В том случае, если подварить шов с обратной стороны не представляется, возможным, пользуются подкладками . Применение подкладок имеет значительные преимущества. Сварщик, не боясь прожогов и протеков, работает уверенно, может увеличить силу сварочного тока, что повышает производительность. Внешний вид шва заметно улучшается. Наплавленный металл имеет плавный переход к основному. В случае сварки швов типа С4 необходимо применять способ сварки погруженной дугой.
5)
Изм. |
Лист |
№ докум. |
Подпись |
Дата |
Лист |
15.01.05. 000 ПЗ |
Сварка сосудов
К сосудам относятся паровые котлы, цистерны, химическая аппаратура. В которых рабочие давление не превышает на 0,7кгс/см2 и выше превышает атмосферное атмосферное. Сосуд обычно состоит из обечаек, сферического днища и патрубков.
В начале из карт собирают листы, которые которые сваривают между собой затем их обвальцовывают по радиусу и сваривают продольным швом.
Сваренные и отвальцованные обечайки собирают между собой с патрубками и сферическим дном кольцевыми швами обратно ступенчатым способом. Патрубки приваривают либо в одном направлении если диаметр патрубков до 200 мм, либо обратно
ступенчатым если диаметр больше 200 мм. Сварные сосуды обязательно проходят специальный контроль на плотность сварных соединений.
Сварка среднеуглеродистых сталей. Такие стали имеют повышенное содержание углерода, который является причиной образования кристаллизационных трещин при сварке, а также малопластичных закалочных структур и трещин в околошовной зоне. Поэтому для повышения стойкости металла шва против образования кристаллизационных трещин следует понизить количество углерода в металле шва. Это достигается применением электродов с пониженным содержанием углерода, а также уменьшением доли участия основного металла в металле шва.
Чтобы снизить вероятность появления закалочных структур, необходимо применять предварительный и сопутствующий подогрев изделия. Надежным способом достижения равнопрочности сварного соединения при низком процентном содержании углерода является дополнительное легирование металла шва марганцем и кремнием.
Среднеуглеродистые стали свариваются электродами УОНИ-13/45, УП-1/45, УП-2/45, ОЗС-2, УОНИ-13/55, К-5А, УОНИ-13/65 и др
Изм. |
Лист |
№ докум. |
Подпись |
Дата |
Лист |
15.01.05. 000 ПЗ |
d1= 3 mm (2.5) J1=(6*3+20)*3=114 A J1=114*0.8=91 A
d2=4 mm (3.5) J2=(6*4+20)*3=176 A J2=176*0.8=114 A
В горизонтальном
d1= 3 mm (2.5) J1= 114*0.8=91 A J1=91*0.8=73 A
d2= 4 mm (3.5) J2=176*0.8=114 A J2=114*0.8=91 A
6)
Изм. |
Лист |
№ докум. |
Подпись |
Дата |
Лист |
15.01.05. 000 ПЗ |
Для освещения следует пользоваться переносной лампой напряжением 12 В. При работах внутри резервуара или при сварке сложной металлической конструкции, а также при сварке емкостей из-под горючих и легковоспламеняющихся жидкостей рядом со сварщиком должен находиться дежурный, обеспечивающий безопасность работ и при необходимости оказывающий сварщику первую помощь.
Перед началом работы необходимо проветрить помещение, проверить наличие на
рабочем месте противопожарных средств, освободить от лишних предметов и легковоспламеняющихся материалов. Запрещается сварка сосудов, находящихся под давлением. Сварка емкостей, содержащих взрывоопасные и горючие вещества, допускается только после их полной очистки и анализа воздушной среды.
Дефекты сварных соединений
При сварке в шве могут образоваться по различным причинам либо несплошности, либо включения. Кроме того форма шва может отличаться от сечения к сечению. Для различных сварочных конструкций установлены нормы (требования) к размерам несплошностей и включений, а также размерам и формам сварного шва в зависимости от назначения конструкций и условий эксплуатации.
Если размеры обнаруженных несплошностей и геометрические размеры шва отвечают указанным в нормативно – технической документации на данное изделие, то соединение не будет дефектным. Следовательно, дефектом называют недопустимое отклонение от требований нормативно – технического документа на конкретное изделие.
Различают следующие сварочные дефекты:
1. Отклонение по ширине и высоте швов, катету, перетяжки швов. Размеры швов не соответствуют требованиям ГОСТа.
2. Подрезы зоны сплавления — дефекты в виде углубления по линии сплавления сварного шва с основным металлом.
3. Пора в сварном шве — дефект сварного шва в виде полости округлой формы, заполненной газом. Цепочка пор — группа пор в сварном шве, расположенных в линию.
4. Свищи — дефекты в виде воронкообразного углубления
5. Непровар — дефект в виде несплавления в сварном соединении вследствие неполного расплавления
Изм. |
Лист |
№ докум. |
Подпись |
Дата |
Лист |
15.01.05. 000 ПЗ |

6. Наплыв на сварном соединении — дефект в виде натекания металла шва на поверхность основного металла или ранее выполненного валика без сплавления с ним.
7. Шлаковые включения — дефекты в виде вкрапления шлака.
8. Трещины — дефекты сварного соединения в виде разрыва в сварном шве и (или) прилегающих к нему зонах.
9. Прожог — дефект в виде сквозного отверстия в сварном шве, образовавшийся в результате вытекания части металла сварочной ванны.
10. Кратер — углубление, образующееся под действием давления пламени при внезапном окончании сварки.
11. Брызги металла — дефекты в виде затвердевших капель на поверхности сварного соединения.
12. Перегрев металла – металл имеет крупнозернистую структуру, металл хрупкий, непрочный, неплотный. Исправляют термообработкой. Причина: сварка пламенем большой мощности.
13. Пережог металла – наличие в структуре металла окисленных зёрен, обладающих малым сцеплением из-за наличия на них плёнки оксидов. Возникает при избытке кислорода в пламени (если это не требуется тех. процессом, как при сварке латуни). Пережжённый металл хрупок и не поддаётся исправлению. Определить его можно по цветам побежалости
Контроль сварных швов
Радиационная дефектоскопия - рентгено- и гаммаграфический метод контроля. Рентгено- и гаммаграфия – это метод получения на рентгеновской, плёнке или экране изображения предмета (изделия), просвечиваемого рентгеновским или гамма-излучением. Он основан на способности рентгеновского и гамма-излучения проходить через непрозрачные предметы, в том числе через металлы, и действовать на рентгеновскую плёнку и некоторые химические элементы, благодаря чему последние
флуоресцируют (светятся).
При этом дефекты, встречающиеся при сварке в теле изделия и чаще всего имеющие характер пустот (не проваров, трещин, раковин, пор и т. д.), на рентгеновской плёнке (на рентгенограммах) имеют вид пятен (раковины, поры) или полос (не провары).
Изм. |
Лист |
№ докум. |
Подпись |
Дата |
Лист |
15.01.05. 000 ПЗ |
Схема просвечивания рентгеновским излучением изделия:
1 - рентгеновская трубка, 2 – футляр со свинцовым экраном, 8 - просвечиваемое изделие, 4 – дефект , 5 - кассета, 6 - экран, 7 –рентгеноплёнка
Ультразвуковой метод контроля. Этот метод основан на способности высокочастотных колебаний частотой около 20000 Гц проникать в металл и отражаться от поверхности дефектов (встретившихся препятствий). Отражённые ультразвуковые колебания имеют ту же скорость, что и прямые, это свойство имеет основное значение в ультразвуковой дефектоскопии.
Узкие направленные пучки ультразвуковых колебаний для целей дефектоскопии получают с помощью пьезоэлектрических пластин кварца или титаната бария (пьезодатчика). Эти кристаллы, помещённые в электрическом поле, имеют обратный пьезоэлектрический эффект, т. е. преобразуют электрические колебания в механические. Таким образом, пьезокристаллы под действием переменного тока высокой частоты (0,8-2,5 МГц) становятся источником ультразвуковых колебаний и создают направленный пучок ультразвуковых волн в контролируемую деталь.
Отражённые ультразвуковые колебания улавливаются искателем (щупом) и затем преобразуются в электрические импульсы. Отражённые электрические колебания через усилитель подаются на осциллограф и вызывают отклонение луча на экране электронной трубки. По виду отклонения судят о характере дефекта.
Ультразвуковой метод контроля сварных соединений:
а - схема, б - общий вид дефектоскопа, в - сигналы на экране осциллографа
Изм. |
Лист |
№ докум. |
Подпись |
Дата |
Лист |
15.01.05. 000 ПЗ |
1 - испытуемый образец, 2 - приёмник, 3 - генератор, 4 - усилитель, 5 - начальный
импульс, 6 - сигнал от дефекта, 7 - ложный сигнал, 8 - генератор развёртки, 9 - излучатель
Магнитный метод дефектоскопии. Сварной шов стального или чугунного изделия покрывают смесью из масла и магнитного железного порошка (размер частиц 5-10 мкм). Изделие намагничивают пропусканием тока через обмотку, состоящую из нескольких витков, намотанных вокруг изделия. Под действием магнитного поля, обтекающего дефект, частицы железного порошка гуще располагаются вокруг дефектов. Этим методом выявляются поверхностные дефекты глубиной до 5-6 мм. Разрешающая способность порошковой дефектоскопии
весьма низкая по сравнению с другими методами контроля, поэтому она эффективна в основном для контроля гладких, чистых, блестящих поверхностей. Магнитным методом можно проверять качество деталей, изготовленных только из ферромагнитных металлов.
Магнитографический метод контроля. При этом методе, разработанном в нашей стране, результаты записываются на магнитную ленту. Сущность этого метода контроля состоит в намагничивании сварного соединения и фиксации магнитного потока на ферромагнитную ленту. Лента накладывается на контролируемое изделие, которое намагничивается импульсным полем. Магнитное поле при наличии дефектов распределяется по поверхности детали по-разному, и соответственно ферромагнитные частицы на ленте намагнитятся в различной степени. Затем ферромагнитная лента снимается с контролируемого изделия и её «протягивают» через воспроизводящее устройство, состоящее из механизма протяжки и осциллографа с усилителем электрических импульсов.
Магнитографический метод контроля сварных соединений:
а - воспроизведение записи на экране дефектоскопа, б - характер импульсов «а экране осциллографа;
1 - кассеты с ферромагнитной плёнкой, 2 - ферромагнитная плёнка, 3 - генератор для стирания записи, 4 - стирающая головка, 5 - воспроизводящая головка, 6 - усилитель, 7 - осциллограф, 8 - лампочка, сигнализирующая о недопустимом дефекте в контролируемом сварномсоединении, 9 - экран осциллографа, 10 - шов без дефекта.
Изм. |
Лист |
№ докум. |
Подпись |
Дата |
Лист |
15.01.05. 000 ПЗ |